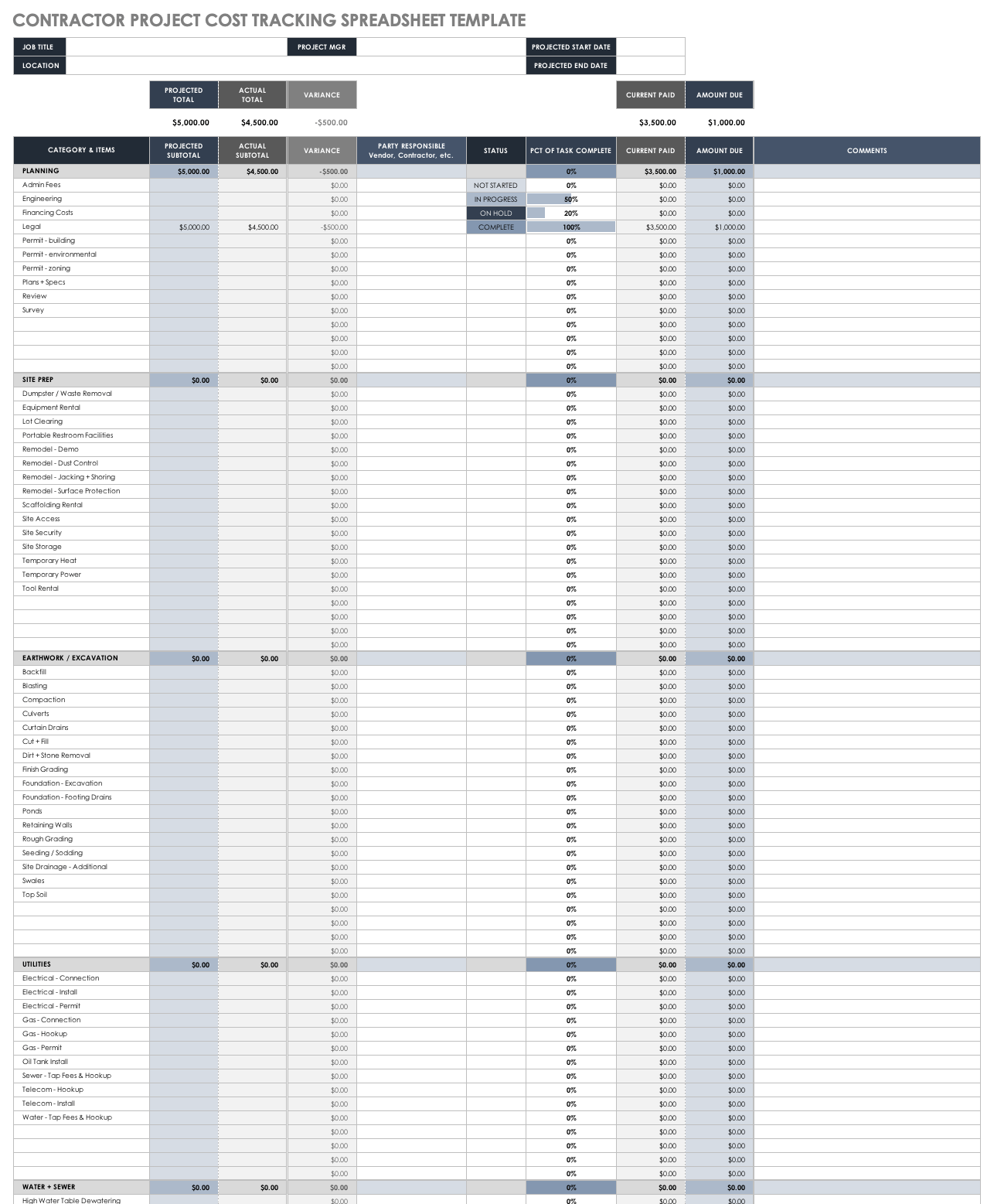
Utilizing such a structure allows for standardized reporting, facilitating cost analysis and comparison across different periods. This consistent approach enables businesses to identify trends, pinpoint areas for potential cost reduction, and make informed decisions about pricing strategies and resource allocation. Ultimately, this structured approach empowers informed decision-making and contributes to improved financial performance.
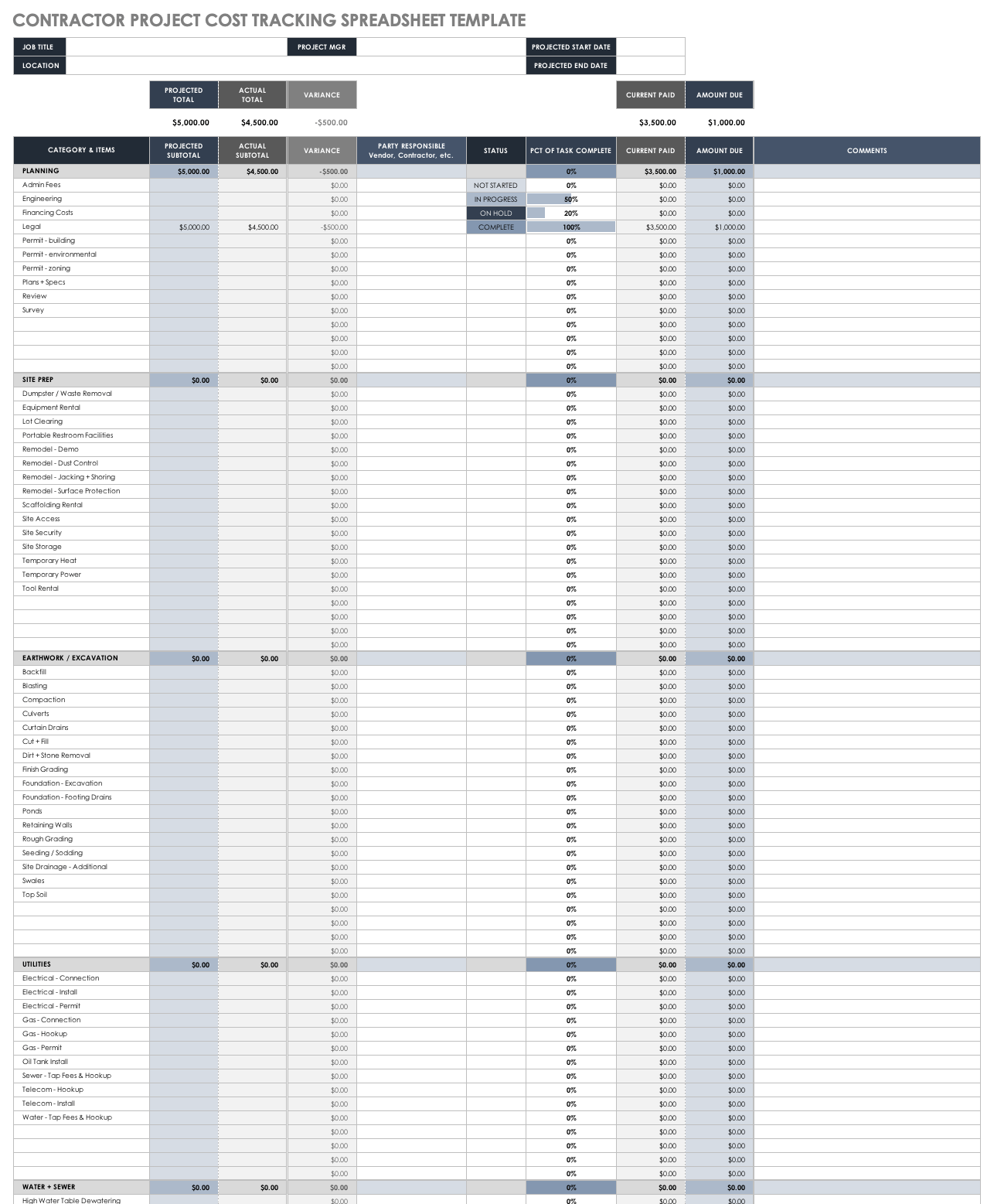
This foundation in cost accounting principles enables a deeper understanding of topics such as inventory valuation, cost control, and the integration of cost accounting with financial reporting. Further exploration of these topics can provide a more comprehensive view of the cost management process.
1. Beginning Work-in-Process Inventory
Beginning work-in-process (WIP) inventory represents the value of partially completed goods at the start of an accounting period. Its inclusion in the statement of cost of goods manufactured template is crucial for accurately calculating the total production costs during that period. The beginning WIP inventory essentially carries forward unfinished production costs from the prior period, ensuring these costs are incorporated into the current period’s cost of goods manufactured. Without accounting for beginning WIP, the cost of goods manufactured would understate the actual production costs, leading to inaccurate financial reporting and potentially flawed business decisions.
Consider a furniture manufacturer. At the beginning of the month, partially assembled chairs might exist on the factory floor. These represent beginning WIP inventory. During the month, additional materials, labor, and overhead costs are incurred to complete these chairs. To determine the total cost of chairs completed during the month, the beginning WIP inventory cost must be added to the costs incurred during the month. For instance, if the beginning WIP inventory is valued at $5,000 and $20,000 in manufacturing costs are added during the month, the total cost accounted for is $25,000. If 500 chairs are completed, the average cost per chair is $50, reflecting both prior and current period costs.
Accurate valuation of beginning WIP inventory is essential for reliable cost accounting. This valuation typically involves detailed tracking of material, labor, and overhead costs assigned to unfinished goods. Challenges can arise when accurately attributing costs to specific WIP items, particularly in complex production environments. However, precise accounting for beginning WIP inventory, along with other cost components, forms the foundation for a robust and informative statement of cost of goods manufactured, enabling informed decision-making regarding pricing, production efficiency, and overall profitability.
2. Manufacturing Costs Added
Manufacturing costs added represent the total expenditure incurred in the production process during a specific period. Within the statement of cost of goods manufactured template, these costs are crucial for determining the value of goods completed during that period. They provide a comprehensive view of the resources consumed in transforming raw materials into finished products, thereby contributing significantly to accurate cost accounting and informed decision-making.
- Direct MaterialsDirect materials encompass all raw materials directly incorporated into the finished product. Examples include wood in furniture manufacturing, steel in automobile production, and fabric in garment making. Accurately tracking direct material costs is essential for determining the cost of goods manufactured. Variances in material prices or usage can significantly impact profitability, underscoring the need for careful monitoring and control within the cost accounting system.
- Direct LaborDirect labor represents the wages and benefits paid to employees directly involved in the production process. This includes assembly line workers, machine operators, and quality control personnel. Direct labor costs are a significant component of manufacturing costs added. Fluctuations in labor rates, productivity levels, or workforce size can directly influence the cost of goods manufactured and, consequently, the overall profitability of the business.
- Manufacturing OverheadManufacturing overhead comprises all indirect costs associated with the production process but not directly traceable to specific products. These costs include factory rent, utilities, depreciation of machinery, and salaries of supervisory staff. Accurate allocation of manufacturing overhead to individual products is crucial for determining the true cost of each item. Misallocation of overhead can lead to inaccurate product costing and potentially flawed pricing strategies.
- Relationship to Work-in-ProcessManufacturing costs added are integral to the calculation of work-in-process (WIP) inventory. The beginning WIP inventory balance is combined with the manufacturing costs added during the period to arrive at the total cost of goods put into production. After subtracting the ending WIP inventory, the result is the cost of goods manufactured. This relationship highlights how manufacturing costs added bridge the gap between beginning and ending WIP, providing a clear picture of the value added during the production process.
Understanding the components of manufacturing costs added provides a deeper understanding of how the statement of cost of goods manufactured template functions as a crucial tool for cost management. Accurate tracking and analysis of these costs offer valuable insights into production efficiency, cost control opportunities, and ultimately, profitability. By effectively managing manufacturing costs added, businesses can optimize their production processes and improve their overall financial performance.
3. Direct Materials Used
Direct materials used represent a crucial component within the statement of cost of goods manufactured template. This figure signifies the value of raw materials directly incorporated into finished goods during a specific accounting period. Accurate accounting for direct materials is essential for determining the true cost of production and, consequently, the overall profitability of manufactured products. The relationship between direct materials used and the statement of cost of goods manufactured is one of direct input and consequential output. Increases in direct material costs directly impact the cost of goods manufactured, influencing pricing decisions and potentially affecting profit margins. Conversely, efficient management and utilization of direct materials can contribute to lower production costs and enhanced profitability.
Consider a bicycle manufacturer. The aluminum used for the frame, the rubber for the tires, and the steel for the gears represent direct materials. If the price of aluminum increases, this directly affects the cost of producing each bicycle, impacting the final cost of goods manufactured. The manufacturer might then need to adjust pricing strategies to maintain desired profit margins. Alternatively, identifying a more cost-effective aluminum supplier or implementing measures to reduce material waste could mitigate the impact of rising material costs. In another scenario, a clothing manufacturer might experience increased demand for a particular line. This increased demand translates to higher consumption of direct materials, such as fabrics and buttons. Accurately tracking this increased material usage within the statement of cost of goods manufactured is vital for understanding the true cost of meeting this heightened demand and for making informed production and pricing decisions.
Understanding the role of direct materials used within the statement of cost of goods manufactured template provides valuable insights into cost drivers within the manufacturing process. Accurate tracking and analysis of direct material costs enable businesses to monitor production efficiency, identify potential cost-saving opportunities, and make data-driven decisions regarding pricing, inventory management, and overall profitability. Challenges can arise when accurately attributing material costs to specific products, especially in complex manufacturing environments with multiple product lines. However, robust inventory management systems and cost accounting practices can mitigate these challenges, ensuring the accurate reflection of direct materials used within the cost of goods manufactured.
4. Direct Labor Costs
Direct labor costs represent the wages, salaries, benefits, and payroll taxes paid to employees directly involved in the production process. Within the statement of cost of goods manufactured template, these costs hold significant weight, directly influencing the final cost of finished goods. This connection is fundamental to understanding production profitability and cost control. Increases in direct labor costs, whether due to rising wages, increased benefit expenses, or higher payroll taxes, directly impact the cost of goods manufactured. Conversely, improvements in labor efficiency, reductions in overtime hours, or effective workforce management can contribute to lower direct labor costs and enhanced profitability.
Consider an automotive assembly plant. Wages paid to assembly line workers, welders, painters, and quality control inspectors on the factory floor constitute direct labor costs. If the plant experiences a period of high demand necessitating overtime hours, direct labor costs will increase, directly impacting the cost of goods manufactured for that period. This increase might necessitate adjustments in vehicle pricing to maintain profitability. Alternatively, implementing automation technologies or improving production line efficiency could mitigate the need for overtime, thus controlling direct labor costs. In another scenario, a furniture manufacturer might decide to invest in training programs to enhance worker skills and productivity. While this investment might initially increase direct labor costs due to training expenses, the long-term benefits of increased productivity can lead to lower per-unit labor costs and improved profitability.
Understanding the relationship between direct labor costs and the statement of cost of goods manufactured template provides valuable insights into cost drivers within the manufacturing environment. Accurate tracking and analysis of direct labor costs, including regular wages, overtime pay, benefits, and payroll taxes, enable businesses to monitor labor efficiency, identify potential cost-saving opportunities, and make informed decisions regarding workforce management, production planning, and pricing strategies. Challenges in tracking direct labor costs can arise when accurately allocating labor hours to specific products or production runs, especially in complex manufacturing settings. However, robust timekeeping systems and cost accounting practices can address these challenges, ensuring the accurate representation of direct labor costs within the statement of cost of goods manufactured, supporting informed decision-making and ultimately, enhancing profitability.
5. Manufacturing Overhead
Manufacturing overhead represents all indirect costs incurred in production, excluding direct materials and direct labor. Within the statement of cost of goods manufactured template, accurate allocation of manufacturing overhead is crucial for determining the complete cost of production. This allocation process links indirect costs to specific products or production lines, enabling a more precise understanding of profitability and cost control. The relationship between manufacturing overhead and the statement of cost of goods manufactured is one of essential inclusion. Manufacturing overhead, comprising costs like factory rent, utilities, depreciation of machinery, and supervisory salaries, must be factored into the overall cost of goods manufactured to accurately represent total production costs. Overlooking or inaccurately allocating these indirect costs can lead to distorted cost figures and potentially misinformed business decisions.
Consider a food processing plant. Costs associated with operating the plant, such as rent, electricity for running machinery, depreciation of processing equipment, and salaries of plant supervisors, represent manufacturing overhead. These costs are not directly tied to a specific batch of processed food but are essential to the overall production process. Accurately allocating these overhead costs to each product line, perhaps based on machine hours or production volume, ensures that the total cost of goods manufactured reflects the full production expense. For instance, if a plant experiences a significant increase in utility costs due to rising energy prices, this increase in manufacturing overhead needs to be reflected in the cost of goods manufactured. This could lead to adjustments in product pricing to maintain profit margins or necessitate efforts to improve energy efficiency within the plant to control overhead costs.
Understanding the nuances of manufacturing overhead allocation within the statement of cost of goods manufactured template is essential for sound cost accounting practices. Methods for allocating overhead, such as activity-based costing, strive to distribute indirect costs fairly and accurately across different products or departments. Challenges arise when dealing with complex production environments or when overhead costs fluctuate significantly. However, accurate overhead allocation, in conjunction with precise accounting for direct materials and direct labor, enables a comprehensive and reliable statement of cost of goods manufactured. This, in turn, facilitates informed decision-making regarding pricing, cost control measures, product profitability analysis, and overall financial performance.
6. Ending Work-in-Process Inventory
Ending work-in-process (WIP) inventory represents the value of partially completed goods remaining in production at the end of an accounting period. Within the statement of cost of goods manufactured template, ending WIP inventory plays a crucial role in accurately calculating the cost of goods manufactured during that period. It reflects the production costs that have been incurred but not yet assigned to finished goods. Understanding the relationship between ending WIP inventory and the statement of cost of goods manufactured is essential for accurate cost accounting and informed decision-making.
- Unfinished ProductionEnding WIP inventory essentially represents unfinished production. It acknowledges that some resources, including direct materials, direct labor, and manufacturing overhead, have been invested in goods that are not yet complete. For example, in a furniture manufacturing setting, partially assembled chairs at the end of the month would constitute ending WIP inventory. These chairs have incurred costs but are not yet ready for sale, thus their associated costs are not included in the cost of goods sold but are carried forward as ending WIP.
- Cost AllocationAccurately valuing ending WIP inventory is crucial for proper cost allocation. This valuation involves estimating the proportion of direct materials, direct labor, and manufacturing overhead assigned to the unfinished goods. For instance, if 50% of the labor required to complete a product has been invested, then 50% of the allocated labor cost for that product is assigned to ending WIP. Accurate cost allocation ensures that costs are appropriately assigned between finished goods and those still in production.
- Impact on Cost of Goods ManufacturedEnding WIP inventory directly affects the calculation of the cost of goods manufactured. It is subtracted from the total cost of work-in-process (beginning WIP inventory plus manufacturing costs added) to arrive at the cost of goods manufactured during the period. This subtraction ensures that only the costs associated with completed goods are included in the cost of goods manufactured. A higher ending WIP inventory will result in a lower cost of goods manufactured, reflecting the fact that more resources remain tied up in unfinished goods.
- Inventory Valuation MethodsDifferent inventory valuation methods, such as weighted-average or FIFO (first-in, first-out), can influence the value of ending WIP inventory. The chosen method impacts how costs are assigned to unfinished goods and, consequently, the reported cost of goods manufactured. Consistency in applying the chosen method is crucial for comparability across accounting periods and for maintaining the integrity of cost accounting data.
In summary, ending WIP inventory is a crucial component of the statement of cost of goods manufactured template. It represents resources invested in unfinished production and its valuation directly impacts the calculated cost of goods manufactured. Accurate accounting for ending WIP inventory, along with other cost components, provides a clear and reliable picture of production costs and supports informed decision-making regarding pricing, inventory management, and overall profitability. By understanding the role of ending WIP inventory within the cost accounting framework, businesses can gain valuable insights into their production processes and enhance their financial performance.
Key Components of a Statement of Cost of Goods Manufactured Template
A statement of cost of goods manufactured template provides a structured approach to calculating the total cost of producing finished goods during a specific period. Several key components contribute to this calculation, each representing a distinct stage or element within the manufacturing process.
1. Beginning Work-in-Process Inventory: This represents the value of partially completed goods at the start of the accounting period. It carries forward costs from the prior period, ensuring these are incorporated into the current period’s calculations.
2. Direct Materials Used: This encompasses the cost of all raw materials directly incorporated into the finished products during the period. Accurate tracking of material usage and costs is essential.
3. Direct Labor Costs: This includes all wages, salaries, benefits, and payroll taxes paid to employees directly involved in the production process. Efficient labor management directly impacts profitability.
4. Manufacturing Overhead: This comprises all indirect production costs, such as factory rent, utilities, and depreciation of machinery. Accurate allocation of overhead is crucial for determining the true cost of each product.
5. Manufacturing Costs Added: This represents the sum of direct materials used, direct labor costs, and manufacturing overhead incurred during the period. This total reflects the value added through the manufacturing process.
6. Ending Work-in-Process Inventory: This represents the value of partially completed goods remaining at the end of the accounting period. It reflects costs incurred but not yet assigned to finished goods.
These components work together within the template to provide a comprehensive view of production costs. Their interrelationships highlight the flow of costs through the manufacturing process, from initial inputs to partially completed and finally, finished goods. Accurate data for each component ensures a reliable calculation of the cost of goods manufactured, supporting informed decision-making related to pricing, cost control, and overall profitability.
How to Create a Statement of Cost of Goods Manufactured
Creating a statement of cost of goods manufactured requires a systematic approach to organizing and calculating production costs. The following steps outline the process:
1. Determine the Beginning Work-in-Process (WIP) Inventory: Obtain the value of partially completed goods at the start of the accounting period. This information is typically available from the previous period’s ending WIP inventory.
2. Calculate Direct Materials Used: Determine the cost of raw materials used directly in production. This involves tracking material purchases, usage, and any returns to suppliers. The formula is: Beginning Raw Materials Inventory + Purchases of Raw Materials – Ending Raw Materials Inventory = Direct Materials Used.
3. Calculate Direct Labor Costs: Compile all costs associated with labor directly involved in production, including wages, salaries, benefits, and payroll taxes. Accurate timekeeping and payroll records are essential for this step.
4. Calculate Manufacturing Overhead: Gather all indirect production costs, such as factory rent, utilities, depreciation of machinery, and supervisory salaries. This often involves allocating indirect costs to specific departments or product lines based on a predetermined allocation method.
5. Calculate Total Manufacturing Costs Added: Sum the direct materials used (Step 2), direct labor costs (Step 3), and manufacturing overhead (Step 4). This figure represents the total manufacturing costs incurred during the period.
6. Determine the Ending Work-in-Process (WIP) Inventory: Calculate the value of partially completed goods remaining at the end of the accounting period. This requires estimating the percentage of completion for these goods and applying the corresponding proportion of costs.
7. Calculate the Cost of Goods Manufactured: Use the following formula: Beginning WIP Inventory (Step 1) + Total Manufacturing Costs Added (Step 5) – Ending WIP Inventory (Step 6) = Cost of Goods Manufactured.
The resulting figure represents the total cost of goods completed during the accounting period. This information is crucial for determining the cost of goods sold and ultimately, the profitability of the manufacturing operations. Accuracy in each step is vital for reliable financial reporting and informed decision-making.
Careful management of resources and cost control are essential for manufacturing success. A structured approach, such as a statement of cost of goods manufactured template, provides the framework for tracking and analyzing production costs. Understanding the key componentsbeginning work-in-process inventory, direct materials, direct labor, manufacturing overhead, and ending work-in-process inventoryallows businesses to accurately assess the total cost of goods manufactured. This understanding provides a foundation for informed decision-making related to pricing strategies, cost optimization initiatives, and resource allocation.
Accurate cost accounting is not merely a compliance exercise but a strategic tool. By diligently applying the principles embodied within a statement of cost of goods manufactured template, organizations gain valuable insights into their production processes. This knowledge empowers them to enhance efficiency, control costs, and ultimately, improve profitability. The ability to analyze and interpret the cost of goods manufactured is essential for navigating the complexities of the manufacturing landscape and achieving sustained success in a competitive market.